
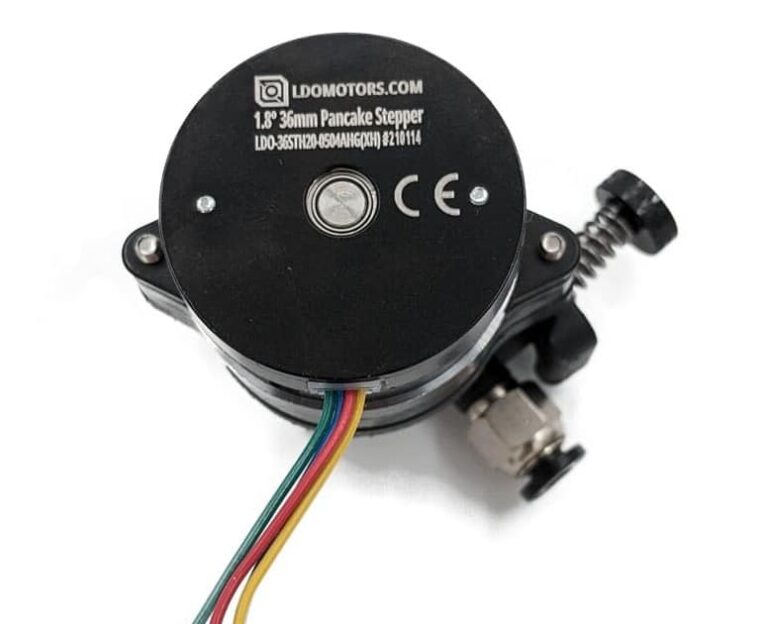

#Orbiter extruder wiring how to#
M566 X400.00 Y400.00 Z10.00 E300.00 C2.00 set maximum instantaneous speed changes (mm/min) This video teaches how to reverse the feeding direction of an extruder by swapping the wires of a stepper motor cable that connect to one of the stepper moto. A brief overview of the Orbiter Filament Sensor from the creator: Before I reached this solution, I have tried many sensor types and sensing. Weight reduced to 135 grams (v1.5 150 grams) Smaller more compact dimensions (11.6 shorter) New motor design offers40 increase in pushing force in real printing conditions and much improved acceleration performance. M350 X16 Y16 Z16 E16 I1 configure microstepping with interpolation M350 C8 I0 configure microstepping without interpolation M569 P4 S0 physical drive 4 goes backwards (Coupler) M569 P3 S1 physical drive 3 goes forwards (E0) M569 P2 S0 physical drive 2 goes backwards (Z axis) M569 P1 S1 physical drive 1 goes forwards (Y axis) Orbiter Extruder Step Motor NEMA14 36mm Round Pancake Motor for Voron Printer. M569 P0 S1 physical drive 0 goes forwards (X axis) Custom request of lead wires or motor cables for RobotDigg Stepper Motors. Features: Shorter drive gears 11mm vs 15 mm Hardened filament drive gears Weight reduced to 135 grams Smaller, more compact dimensions (11. I have tried different currents 1400mA, 1000mA, 900mA and 700mA but still doing the same. The LDO Orbiter V2.0 high precision direct drive extruder designed by Dr. Retraction: 1.2mm (for the volcano V6 hotend) Maximum instantaneous speed change (jerk): 300 mm/min(RRF), 5 (Marlin) Stepps: 655 stepps / mm 16 micro-stepping (for the 7.5:1 gearing ratio) I have put the configuraton for the extruder as per instructions: I have also tried swapping the cables but is not working either.

The connections are B, A, A, B on the duet, the same for my motor. Nor the board has problem because for ease of practicing I have tried driver3 and driver0. This section covers the wiring for the new extruder wiring assembly. I have bought 4 motors from Wantai (36BYGH218, 1.8A, 1.8deg/step)and tested them all, so I do not think it is the motor's problem, because they are all doing the same noise like ggrrrrr, loosing steps. Unfortunately I am having problems with the motor. I have just instaled the new extruder, "The orbiter", for minimizing the weight. The Orbiter extruder really performed well in that scenario as it was still extruding. These are more expensive than PLA or ABS but their strength is unmatched.I need some help. Rat Rig provides a great wiring diagram for the wiring process. These filaments are typically able to be printed without an enclosure and need a high nozzle temp of 230-250C and bed temp up to 80C. 3 Months Warranty - Our warranty covers any. Nylon Filaments Nylon is a very STRONG filament where durability and layer adhesion is needed. If they do not, you will need to splice the wires into the existing ones on your 3D printer. OS2 Nylon SLS Printing(only compatible with orbiter v2.0 extruder) x1.ABS should be printed inside an enclosure to ensure part strength and reduce warping. ABS Filaments ABS is a very strong plastic with high-temperature resistance (100C+).PETG filaments have excellent layer adhesion and handle heat up to 70-80C for higher ambient temperatures. I know I have to change VREFs on the board and change eSteps, but other than that it seems like a straightforward install.
#Orbiter extruder wiring install#
PETG Filaments PETG is an alternative to ABS for those who do not have an enclosure to print in. Has anyone installed an Orbiter direct extruder : r/ender5plus Has anyone installed an Orbiter direct extruder I'm looking to install one and wanted to check if anyone else had done it.PLA Filaments PLA is a biodegradable, renewable plastic that is easy to print and affordable.
